
SPI FINISH STANDARD | SURFACE ROUGHNESS RA (ΜM) | FINISHING METHOD | FNISHING LOOK | STEELS SUGGESTED |
---|---|---|---|---|
SPI A1 | 0.012 to 0.025 | 6000 Grit Diamond | Super High Glossy finish | S136 (54HRC) or 8407(52HRC) |
SPI A2 | 0.012 to 0.025 | 3000 Grit Diamond | High Glossy finish | S136 (54HRC) or 8407(52HRC) |
SPI A3 | 0.05 to 0.10 | 1200 Grit Diamond | Normal Glossy finish | S136 (300HB) or 718H |
SPI B1 | 0.05 to 0.10 | 600 Grit Paper | Fine Semi-glossy finish | 718H |
SPI B2 | 0.10 to 0.15 | 400 Grit Paper | Medium Semi-glossy finish | 718H |
SPI B3 | 0.28 to 0.32 | 320 Grit Paper | Normal Semi-glossy finish | 718H |
SPI C1 | 0.35 to 0.40 | 600 Grit Stone | Fine Matte finish | 718H |
SPI C2 | 0.45 to 0.55 | 400 Grit Stone | Medium Matte finish | 718H |
SPI C3 | 0.63 to 0.70 | 320 Grit Stone | Normal Matte finish | 718H |
SPI D1 | 0.80 to 1.00 | Dry Blast Glass Bead | Satin Textured finish | 718H |
SPI D2 | 1.00 to 2.80 | Dry Blast | Dull Textured finish | 718H |
SPI D1 | 3.20 to 18.0 | Dry Blast | Rough Textured finish | 718H |
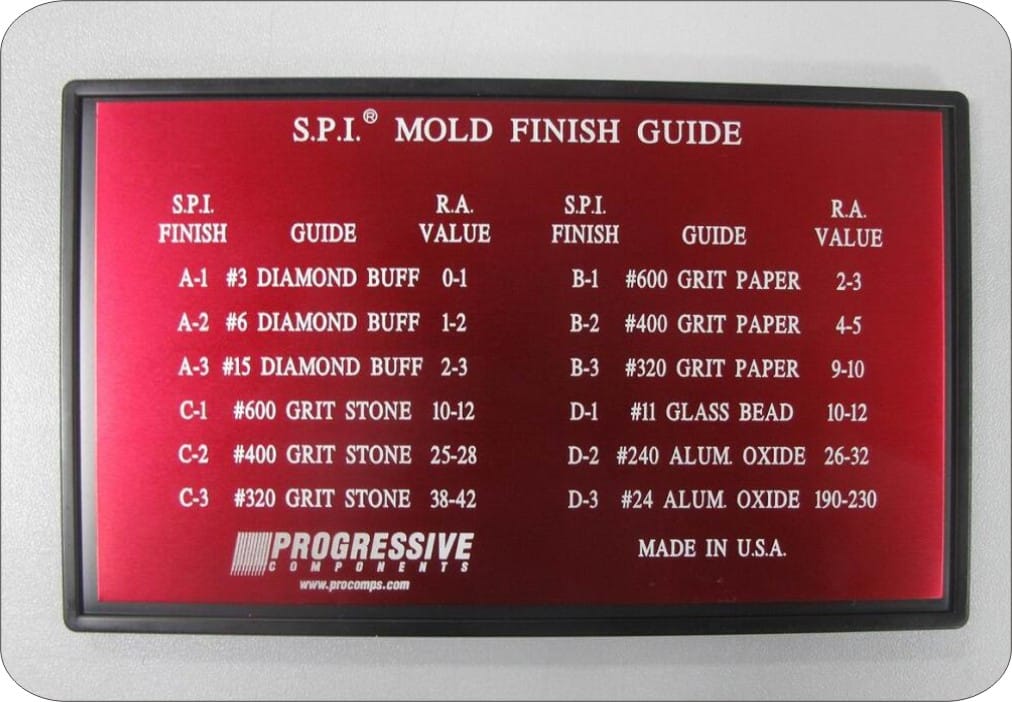
VDI parameter | Instructions | Application | Surface roughness (Ra um) |
12 | 600 oil stone | Low Polishing Requirements | 0.40 |
15 | 400 oil stone | Low Polishing Requirements | 0.56 |
18 | #24 Sandblasting (coarse glass beads) | Sandblasting (coarse glass beads) | 0.80 |
21 | #24 Sandblasting (coarse glass beads) | 24 Oxide Sandblasting | 1.12 |
24 | #24 Sandblasting (coarse glass beads) | 24 Oxide Sandblasting | 1.60 |
27 | #24 Sandblasting (coarse glass beads) | Dull Finish | 2.24 |
30 | #24 Oxide Sandblasting (coarse glass beads) | Dull Finish | 3.15 |
33 | #24 OxideSandblasting (coarse glass beads) | Dull Finish | 4.50 |
36 | #24 Oxide Sandblasting (coarse glass beads) | Dull Finish | 6.30 |
39 | #24 OxideSandblasting (coarse glass beads) | Dull Finish | 9.00 |
42 | #24 Oxide Sandblasting (coarse glass beads) | Dull Finish | 12.50 |
45 | #24 Oxide Sandblasting (coarse glass beads) | Dull Finish | 18.00 |
The molds used in injection molding processes are mostly made of aluminum and/or steel. As long as there are imperfections on the mold surface, even small imperfections can be reflected in the final molded parts. If these marks are not removed by sandblasting or polishing, the mechanical tool marks will remain on the finished product. In most cases, if the interior of the part is not visible to the naked eye, there is no problem with tool marks, which will not affect the appearance or function of the part
However, those exposed surfaces often require additional processing. Almost all molds are polished to varying degrees, but of course, the more refined the polishing, the higher the cost of the mold and the longer the manufacturing time of the mold.
The key factors that determine surface treatment
Injection molding processes have different surface treatment processes than parts produced by machining or 3D printing. The surface finishing of the latter two is performed after the parts are manufactured, which is a post-processing step. For injection molding processes, the mold itself must undergo such treatment (or add texture), and the molded parts are the finished products. For example, if the finished part requires a matte surface, the interior of the mold must be textured first to achieve the matte effect on the molded part. The key factors determining surface treatment are the following two factors:
Improve the appearance of parts
The designer of the part may choose the texture of the finished product based on different aesthetic considerations. A smooth or matte texture on the surface of the part not only improves the appearance and gives a sense of quality, but also covers minor defects such as flow lines, weaves, dents, or shadow marks caused during the injection molding process. From a commercial perspective, parts with better surface finish are also more attractive to customers.
Improve part function
The texture treatment of the part surface can improve the adhesion of paint or stickers. For example, parts with a matte texture are easier to paint, and the durability of the paint is also better. The matte texture is also more suitable for sticking labels. Texture treatment can also make parts easier to grip. By surface treating the mold, we can also avoid over-injection or under-injection defects of plastic parts. A well-designed part with texture treatment can also help discharge air inside the mold to avoid trapped air.